Seit 30 Jahren 3D-Druck! Ihr Rapid Prototyping / Additive Manufacturing Dienstleister seit 1991. Der Spezialist für komplexe und kleinste Teile mittels 3D-Druck in höchster Qualität. Wir bieten eine grosse Auswahl an Standardmaterialien.
Die PROFORM AG ist Ihr Partner für die rasche Fertigung von Prototypen und Kleinserien in Kunststoff mit folgenden Verfahren:
3D-Druck / Additive Manufacturing – Stereolithographie – Fused Deposition Modeling (FDM)
Vakuumgiessen – Polyurethan – Silikon
Rapid Tooling – Thermoplaste
Die langjährigen Erfahrungen, unser spezielles Know How und die spezifische Ausstattung machen uns zum Spezialisten für die besonders komplizierten kleineren und kleinsten Teile.
Dank einer sehr breiten, kontinuierlich optimierten Materialpalette kann die PROFORM AG mit ihrer leistungsfähigen Infrastruktur einen grossen Anwendungsbereich abdecken und Ihnen massgeschneiderte Lösungen für Ihre Bedürfnisse / Anforderungen bieten.
Unsere Kunden kommen aus den Bereichen der Medizintechnik, der Elektronik, der Uhrenindustrie, von wissenschaftlichen Einrichtungen sowie aus der Automobil- und der Konsumgüterindustrie.
In einer Zeit mit hohen Innovationsraten und immer kürzeren Innovationszyklen hilft Rapid Prototyping die Entwicklung zu unterstützen und zu beschleunigen und ermöglicht die wirtschaftliche Produktion von kleinen Serien.
►Download Firmenbroschüre >>>
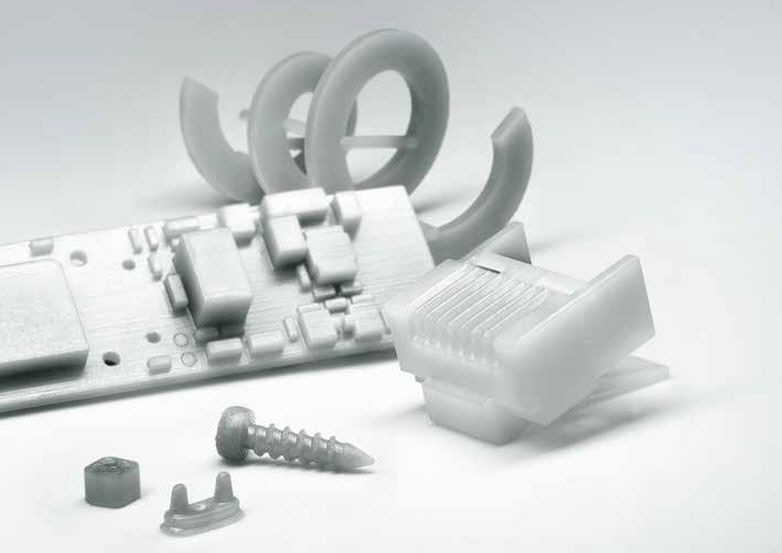
VERFAHREN
Wir bieten folgenden Verfahren an: • 3D-Druck / Additive Manufacturing >>> • Vakuumgiessen >>> • Rapid Tooling >>>
3D-Druck / Additive Manufacturing
Stereolithographie: Komplexe und kleinste Prototypen aus Epoxyharzen mittels 3D-Druck in hoher Auflösung und exzellenter Oberflächenqualität.
Fused Deposition Modeling (FDM): Funktionsfähige Einzelmodelle oder Kleinserienteile aus den bekannten Serienmaterialien PC, ABS, PC-ABS Blend und ESD7.
Stereolithographie - Infos >>> Stereolithographie ist das 3D-Druckverfahren mit den qualitativ besten Ergebnissen. Mit Stereolithographie können sehr schnell einzelne Prototypen oder Kleinserien mit einer hohen Genauigkeit und exzellenter Oberflächenqualität hergestellt werden.
Einsatz Stereolithographieprototypen aus speziellen Epoxyharzen dienen zur Verifikation und Optimierung eines Designs, zu ersten Funktions- und Montageprüfungen, zu Präsentations- und Marketingzwecken. Dank der hohen erreichbaren Präzision von typischerweise 0.1% und der guten Oberflächenqualität, die durch eine weitere Nacharbeit (Polieren, Beschichten) weiter vergütet werden kann, dienen sie insbesondere auch als Urmodelle für eine Reihe von Abgiessprozessen, wie Vakuumguss, Rapid Tooling und Metallguss.
Technologie Ausgangspunkt zur Fertigung ist eine STL-Datei, die den Prototypen digital beschreibt und die mittels spezieller Software des Herstellers in eine Vielzahl von Objektquerschnitten (Slices) von typischerweise 0.025 – 0.1 mm umgewandelt wird.
Ein computergesteuerter Laserstrahl “zeichnet“ nun diese Schichten sukzessive auf die Oberfläche eines flüssigen photopolymeren Kunststoffs, wobei unter Zeichnen das Auslösen einer lokalen chemischen Reaktion (Polymerisation) zu verstehen ist. Die sogenannte Polymerisationstiefe übertrifft dabei die gewählte Schichtdicke, um einen guten chemischen Verbund zwischen den Schichten zu gewährleisten. Nach jeder Härtungsphase wird das auf einer vertikal beweglichen Plattform (durch mitgebaute Stützen) fixierte Objekt um eine Schichtdicke abgesenkt und mit einer frischen Schicht flüssigen Harzes beschichtet, worauf deren Laserhärtung beginnen kann. Nach Beendigung des Bauprozesses werden die Stützen entfernt, wird das Teilgereinigt, in einem UV-Strahler nachgehärtet und anschliessend fertig verputzt.
Materialien Um einen breiten Anwendungsbereich abdecken zu können, sind bei der PROFORM AG dauernd 5 Materialien im Einsatz, mit denen auch erhöhten Anforderugen hinsichtlich mechanischer Festigkeit und Schlagzähigkeit, Temperatur- und Feuchtigkeitsbeständigkeit, sowie Auflösung entsprochen werden kann. Unser Resin Selector Guide hilft Ihnen, das optimale Material für Ihre Anwendung zu finden! Zusätzliche technische Details zu den Materialien finden Sie auf unserer Übersichtstabelle.
Technische Ausstattung 10 Stereolithographieanlagen mit max. Bauraumgrösse von: 254x252x254 mm³ oder 380x380x250 mm³ oder 350x350x400 mm³ (ProJet 7000, Viper si2, SLA-3500)
Lieferzeiten 1 – 4 Arbeitstage
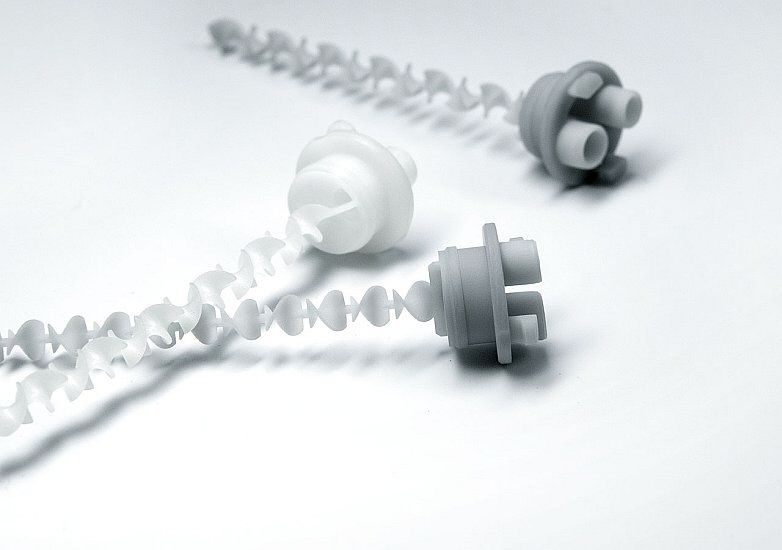
FDM (Fused Deposition Modeling) - Infos >>>
FDM (Fused Deposition Modeling)–Prototypen werden vor allem als funktionsfähige Einzelmodelle oder Kleinserienteile aus den bekannten Serienmaterialien PC und PC-ABS Blend verwendet. Die Oberfläche von FDM–Bauteilen ist strukturierter als z.B. die von Stereolithographie–Teilen.
Einsatz FDM-Modelle erfüllen hohe Anforderungen bezüglich mechanischer Festigkeit, Schlagzähigkeit, chemischer Resistenz oder Wärmeformbeständigkeit. ABS – Modelle werden auch als verlorene, ausbrennbare Urmodelle im Feinguss verwendet.
Technologie Bei der FDM-Technologie handelt es sich um ein Extrusionsverfahren. Wie auch bei der Stereolithographie wird das Modell mittels einer speziellen Software in Position gebracht und in Schichten zerlegt (Slicing). Bei überhängenden Teilen wird ein sogenannter Support erzeugt, eine Stützstruktur, die nach dem Bau wieder entfernt wird. Dei Materialien stehen in Drahtform zur Verfügung. So kann das Material leicht zum Druckkopf geführt werden, wo es aufgeschmolzen und dann auf die Bauplattform extrudiert wird.
Materialien Polycarbonat (PC): für Funktionsmodelle mit höchster Schlagzähigkeit und guter Wärmeformbeständigkeit (125°C). ABS: für Funktionsmodelle mit guter mechanischer Festigkeit und chemischer Resistenz. PC-ABS Blend (schwarz): vereinigt gute mechanische und chemische Resistenz und kann mit einem auswaschbaren Stützmaterial (Water Works Techologie) verarbeitet werden, was insbesondere bei komplexen Modellen ein grosser Vorteil ist.
Technische Ausstattung FORTUS 400mc Large Anlage der Firma Stratasys (max. Bauraumgrösse 408x355x408 mm)
Lieferzeiten 1 – 4 Arbeitstage
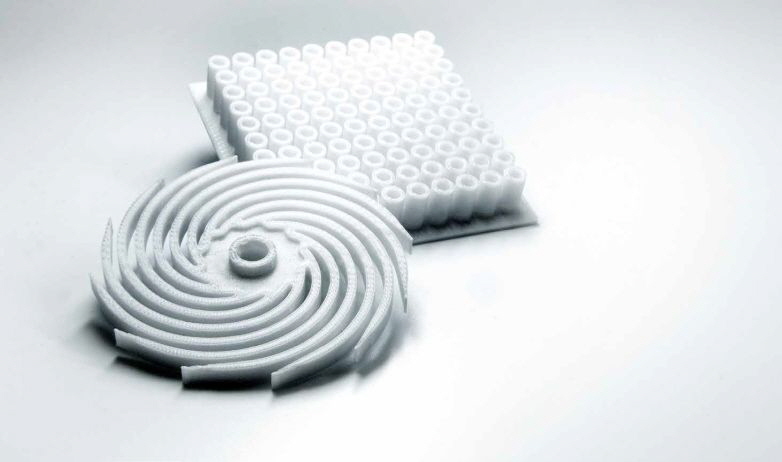
Vakuumgiessen
Für Kleinserien und/oder bei speziellen Materialanforderungen (mechanisch, thermisch, visuell,..) ist der Vakuumguss ein schnelles und kostengünstiges Verfahren.
Wenn eine kleine Serie benötigt wird oder spezielle Materialanforderungen bestehen, ist der Silikon – / Vakuumguss ein schnelles und kostengünstiges Verfahren.
Transparente und farbige Teile oder Kombinationen von harten und weichen gummiartigen Teilen oder das Übergiessen von Werkstücken aus anderen Materialien, vieles ist beim Vakuumgiessen möglich.
Einsatz Häufig reicht ein einzelner Prototyp in der Produkteentwicklung für die beteiligten Projektpartner (Designer, Entwickler, Werkzeugmacher, Marketingfachleute, etc.) nicht aus. Ausgehend von einem Einzelprototypen, typischerweise einem Stereolithographie-Urmodell, eröffnet dieses Verfahren über eine Silikonform einen raschen und kostengünstigen Zugang zu einer Kleinserie von typischerweise bis zu 20 Teilen pro Form und zu einer Palette von thermoplast- oder elastomerähnlichen duroplastischen Materialien mit angepassten Eigenschaften.
Besonders geeignet für Vorserien oder Kleinserien mit typischerweise 5 – 100 Stück.
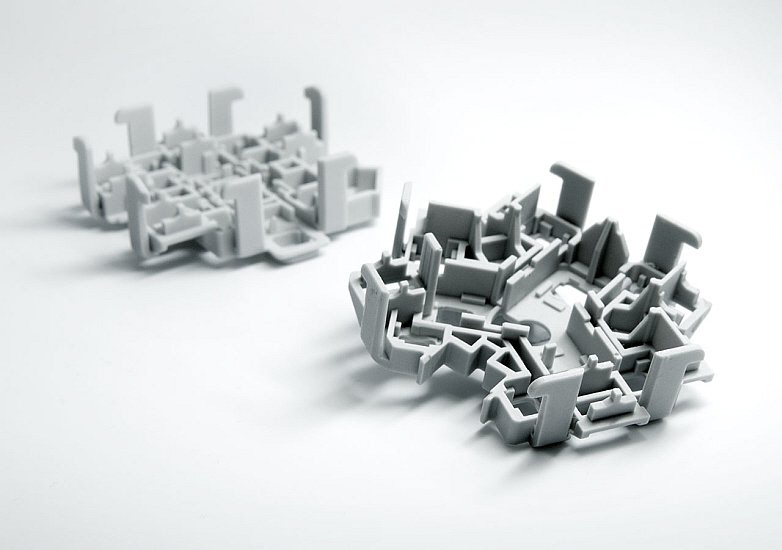
Technologie
Vakuumguss: Der fertig verputzte Stereolithographieprototyp wird in eine Silikonkautschukmasse eingegossen, welche sich in der Folge verfestigt. Nach der Aushärtung wird die Silikonform entlang der Formtrennebene aufgeschnitten und das Urmodell entfernt. Die Innenflächen der Form werden mit einem Antihaftmittel behandelt, dann wird die Form wieder geschlossen und in der unteren Kammer der Giessmaschine evakuiert. Gleichzeitig wird in der oberen Kammer das Giessharz (noch in zwei flüssigen Komponenten) ebenfalls evakuiert. Die zwei Komponenten werden zusammen gemischt und in die Form gegossen. Nach einer gewissen Aushärtezeit kann der Giessling der Form entnommen werden, worauf die Form für den nächsten Abguss vorbereitet wird. Pro Form können je nach Komplexität der Teile ca. 15 -25 Abgüsse angefertigt werden. Es bleibt das Finish und eine allfällige Oberflächenbehandlung des abgegossenen Teils. Silikonguss: Im Unterschied zu Vakuumguss wird beim Silikonguss mittels Stereolithographie eine harte Epoxy-Form hergestellt, ein Urmodell ist nicht notwendig. In diese Form wird dann unter Vakuum das Silikon gegossen. Die möglichen Geometrien sind beim Silikonguss etwas eingeschränkter als beim klassischen Vakuumguss. Die Silikongussteile sind auch in den Grundfarben einfärbbar. Aus der riesigen Zahl an verfügbaren Silikonen sind nur sehr wenige Silikone für diese Technik geeignet.
Materialien Uns steht eine grosse Auswahl an Materialien mit verschiedenen Eigenschaften zur Verfügung. Nachfolgend eine grobe Klassierung: Polyurethanharze (PU): mit verschiedensten elastomer- und thermoplastähnlichen Materialeigenschaften (Härten Shore A 25 – D 85)
Silikone (RTV): diverse Shore A-Härten (A 28 – A 60)
Weitere technische Informationen zu den bei uns im Vakuumguss standardmässig eingesetzten Materialien, finden Sie auf den Übersichtsblättern für harte und halbharte Materialien und für elastische Materialien.
Technische Ausstattung Mehrere Vakuumgiessanlagen von SLM im Einsatz (max. Formgrösse ca. 580x500x450 mm)
Lieferzeiten 4 – 6 Arbeitstage
â–ºWeitere Informationen finden Sie hier.
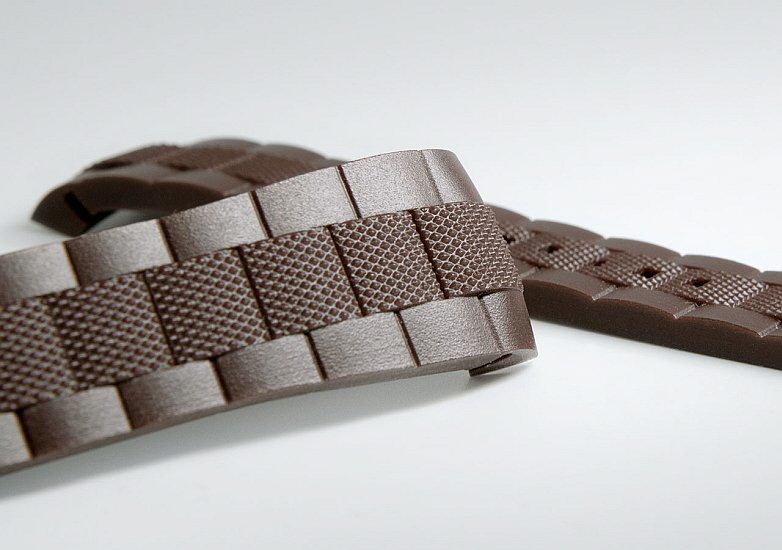
Rapid Tooling
Grössere Stückzahlen von kleinen, einfacheren Bauteilen können mit dem Rapid Tooling Verfahren in Serienmaterialien (zB ABS, PMMA, PE, PP, PA6, PA66, PC) hergestellt werden.
Einsatz Dieses Verfahren kommt vor allem bei kleineren, wenig hinterschnittenen Teilen bis zu einer Grösse von ca. 150x100x100 mm zur Anwendung, wenn Stückzahlen von typischerweise 100 – 2000 Stück in Serienmaterialien benötigt werden.
Technologie Ausgangspunkt ist ein präzises Stereolithographie-Urmodell mit hoher Oberflächenqualität. Nach Festlegung der Trennebenen wird dieses in zwei Schritten durch ein metallgefülltes Epoxyharz umgossen, das zu einem metallähnlichen Werkstoff aushärtet. Anschliessend wird das Urmodell entfernt, werden Anspritzpunkte festgelegt und das Werkzeug, wenn nötig, anderweitig nachbearbeitet.
Das Spritzgiessen erfolgt auf einer Kolbenmaschine, wobei die Teile in der Regel manuell entformt werden. Daraus ergibt sich, je nach Teilegeometrie, eine Zykluszeit von typischerweise 1 - 5 Minuten.
Materialien Thermoplaste wie ABS, PMMA, PE, PP, PA6, PA66, PC, etc.
Lieferzeiten 2 – 4 Wochen
â–ºWeitere Informationen finden Sie hier.
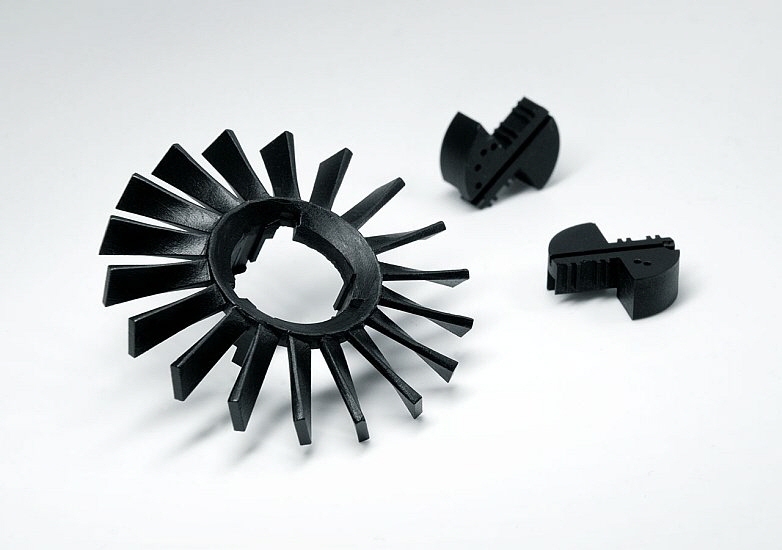
REFERENZEN
Creaholic, Biel «In all den Jahren, in denen wir schon zusammen arbeiten, ist mir kaum je eine Firma so positiv aufgefallen wie die PROFORM. Absolute Zuverlässigkeit und beste Qualität machen es zur Freude, mit ihnen zu arbeiten.»
Reichle & De-Massari AG, Wetzikon «Um die Entwicklungszeiten neuer Produkte möglichst kurz zu halten, ist es für uns ein Muss, schnell und präzise Prototypen in einem frühen Entwicklungsstadium zur Verfügung zu haben.
In der Firma PROFORM haben wir einen Dienstleister gefunden, der bestrebt ist, unsere sehr feinen und komplexen Prototypen mit den neuesten Materialien und Maschinen, äusserst präzise und in unglaublich kurzer Zeit (2 – 3 Tage) herzustellen.»
Olivetti, Yverdon «Die Schnelligkeit und die Flexibilität dieser Technologie erscheinen uns ohne Grenzen und erlaubt es uns, das Konzept bis zum letzten Moment vor der Herstellung der Produktionswerkzeuge abzuändern. Es war für uns sehr beruhigend zu wissen, dass PROFORM ihre Versprechen hinsichtlich Termin und Qualität jedesmal erfüllt.»
Siemens Schweiz AG, Zug « Für unsere Projekt- und Entwicklungsteams, sowie für unseren Marketing / Verkauf ist es von hoher Wichtigkeit, in einer zunehmend von Termin- und Kostendruck geprägten Zeit, einen starken, zuverlässigen Partner im Prototypenherstellverfahren zu haben. Dabei spielt der Gesamteindruck, die Oberflächengüte und die Masshaltigkeit der Prototypenteile eine entscheidende Rolle.
In der Firma PROFORM haben wir einen starken Partner gefunden. Für die Firma Siemens Metering and Siemens Building Technologies, Landis&Stäfa Divison wurden unsere Erwartungen hinsichtlich der Lieferprformance der Teile sowie der Mitarbeit in den verschiedenen Projekten sehr gut erfüllt.»
Logitech SA, Romanel «Les interactions entre la mécanique, l’électronique et l’optique composant nos produits creent des phénomènes complexes qui sont difficiles d’imaginer et d’améliorer sans un modèle fonctionnel.
Grâce à PROFORM nous pouvons obtenir en quelques jours un prototype ce qui nous permet de corriger les erreurs et d’améliorer notre concept. Cette methode de travail permet non seulement de réduire le temps de cycle mais augmente aussi leur efficacité et en réduit le nombre.»
SHOW CASE
Pflanzendünger perfekt dosiert
Als die Firma Hauert HBG Dünger AG nach einer praktischen neuen Lösung für die Dosierung ihrer Flüssigdünger suchte, wandte sie sich an Creaholic und deren Partner Proform. In kurzer Zeit entstand ein komplett neues System - auch dank der hochwertigen Stereolithographie-Prototypen.
Entwicklung eines Designkonzeptes Verschiedenste mögliche Designkonzepte für ein einfacheres, saubereres Dosieren des Flüssigdüngers wurden von der Creaholic - einem Team aus Ingenieuren und Designern aus unterschiedlichsten Fachgebieten - entwickelt.
Die funktionalen Prototypen wurden mit dem qualitativ hochwertigsten additiven Herstellungsverfahren, der laserbasierten Stereolithographie durch die Proform AG produziert.
Die sehr hohen Anforderungen an Auflösung, Dichtheit und Transparenz, welche die Überprüfung der Dosierfunktionalität inklusive beweglicher Teile ermöglichte, werden durch kein anderes additives Verfahren erreicht.
Markteinführung gelingt innert einem Jahr Auch für grössere Stückzahlen oder optisch schöne Teile ist das Additive Manufacturing mittels Stereolithographie mit professionellen Maschinen und dem nötigen Know-How oft die beste und einzige Lösung. Vom Projektstart bis zur Markteinführung hat es weniger als ein Jahr gedauert.
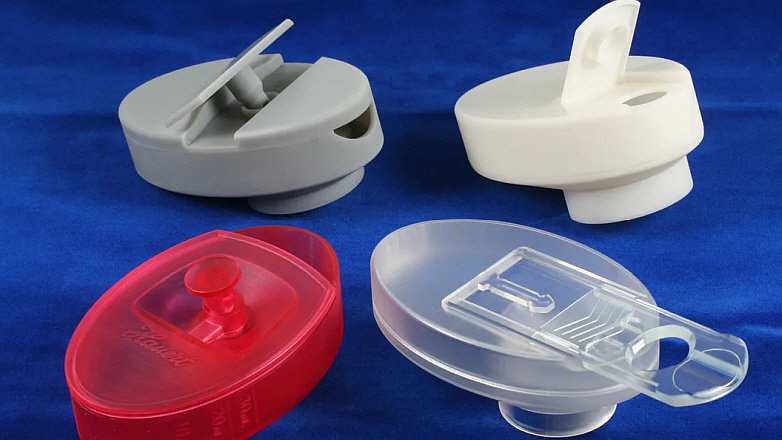 Stereolithographiemodelle diverser Entwicklungsstufen des Dosierdeckels |